Article
Biosafety Cabinet Types
4/16/2024 Seth De Penning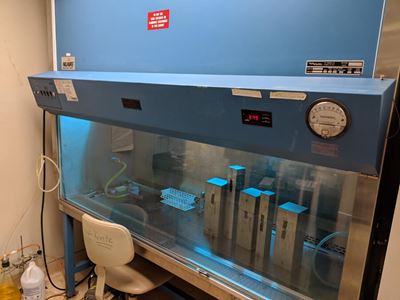
Biosafety cabinets (BSCs) are essential tools in laboratories, designed to safeguard laboratory personnel, the work conducted within, and the surrounding environment from exposure to infectious agents and hazardous materials. This article delves into the various types of biosafety cabinets, explaining their unique functions and operational mechanics.
Understanding Biosafety Cabinets:
A biosafety cabinet is a ventilated enclosure offering protection by containment, employing HEPA-filtered laminar airflow to prevent airborne contaminants from escaping the cabinet. The effectiveness of a BSC relies on its ability to manage airflows meticulously to create barriers against contamination.
Types of Biosafety Cabinets:
Class I BSC
Class I cabinets provide personnel and environmental protection by filtering air through a HEPA filter before it is exhausted. These cabinets do not protect the product within from potential contamination and are suitable for general manipulations of low-to-moderate risk agents where product sterility is not a priority.
Class II BSCs:
Class II cabinets are designed to protect the product, personnel, and environment, making them ideal for handling microbiological and biotechnological materials with a requirement for aseptic conditions.
- Type A1 BSCs:
Often used in clinical and research laboratories for standard microbiological work with no chemical evaporation. Type A1 cabinets maintain a minimum inflow velocity of 75 feet per minute and recirculate 70% of the air while exhausting 30% outdoors after filtration. They are not suitable for handling volatile or toxic chemicals.
- Type A2 BSCs:
Similar to Type A1 but with increased inflow velocity of 100 feet per minute, enhancing containment. Type A2 cabinets can handle minute amounts of volatile chemicals if vented with an appropriate thimble (canopy) connection to the facility’s HVAC system. This type is prevalent in pharmaceutical compounding and biotechnology sectors. Learn more about Type A2 BSCs.
- Type B1 BSCs:
Designed for work involving minute quantities of toxic chemicals and radionuclides as long as these operations occur toward the rear of the work area, directly exhausted outside. Type B1 maintains a balance where 70% of air is exhausted and 30% is recirculated, both through HEPA filters. Learn more about Type B1 BSCs.
- Type B2 BSCs:
Also known as Total Exhaust Cabinets, these are suitable for handling significant quantities of toxic chemicals and radionuclides. They maintain a minimum inflow of 100 feet per minute and exhaust 100% of the air. All inflow and downflow air is ducted out of the building, providing no recirculation within the cabinet. Learn more about Type B2 BSCs.
- Type C1 BSCs:
A versatile cabinet that functions under both Type A and Type B conditions with a switch to change between modes depending on the chemicals used. This type provides flexibility in laboratories that handle both biological samples and chemicals, adjusting the exhaust accordingly. Learn more about Type C1 BSCs.
Class III BSCs:
Offering the highest level of protection, Class III cabinets are gas-tight enclosures used with high-risk microbiological agents and hazardous chemicals. They operate under negative pressure, and materials are manipulated through attached gloves. Learn more about Class III BSCs.
Conclusion:
Selecting the appropriate type of biosafety cabinet is crucial for the safety of laboratory operations. Each type of Class II BSC offers different levels of protection and is suited for various applications, from simple microbiological research to handling hazardous substances. It’s essential for laboratory personnel to understand the capabilities and limitations of each BSC type to ensure maximum protection and operational efficiency. Regular certification and maintenance of these cabinets are also critical to maintain their protective functionality and compliance with biosafety standards.